Does every home master know how to properly solder wires with a soldering iron? This type of connection is the most effective than their twisting. The latter method is generally prohibited by the PUE. On the one hand, it seems that the soldering process itself is quite simple: just dip the tip in rosin, pick up some solder and connect the wires.
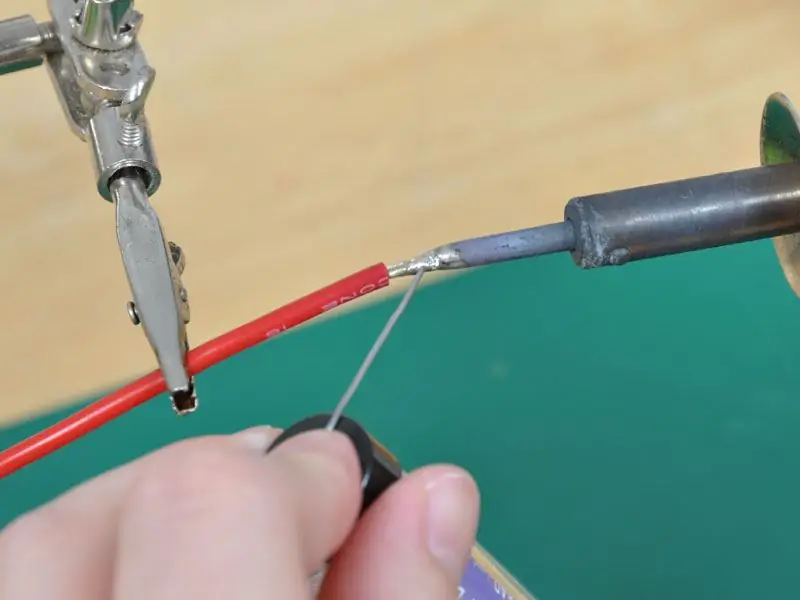
In fact, this kind of work requires certain skills that only come with experience. Between the masters of this business there is a difference in the quality of soldering, and a very significant one. To understand the whole point, it is worth delving into this area.
Types of soldering irons
There are several varieties of this kind of instruments:
- Electric - powered by regular home power.
- Gas - uses a gas burner.
- Thermoair - here the work is done by air flow.
- Induction - the tip is heated by a magnetic field.
In everyday life mostlyuse electric soldering irons. They differ in power among themselves, which is important for carrying out various works.
May need
Actually, for work you can not do without the soldering iron itself. You will also need rosin or any other fluxes, solder. With a tool stand it will be noticeably easier. In addition, thinking about how to properly solder the wires with a soldering iron to the microcircuit, we can come to the conclusion: the work will be greatly facilitated with the presence of additional devices and materials:
- Metal stand as a work surface on which the soldering process itself will be carried out.
- Braid of thin copper strands. It can remove excess solder.
- Pliers, clamps or tweezers. They are convenient to hold heated metal parts.
- File. Sometimes you have to sharpen the tip of the soldering iron.
- Insulating tape, heat shrink tubing provide core insulation.
- Alcohol to wash off excess flux.
In addition, you should be well prepared for the work itself.
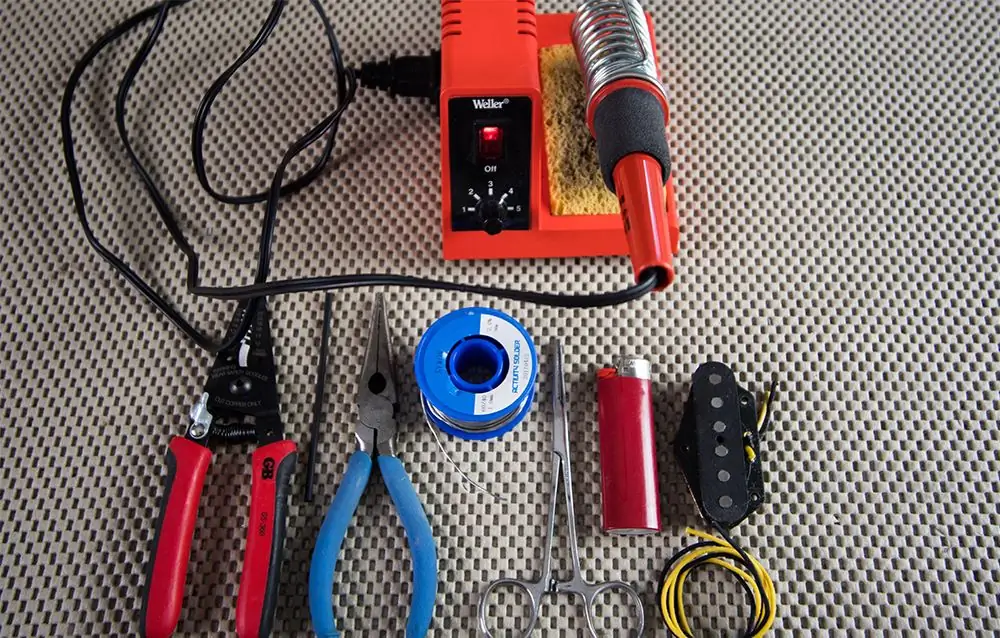
First, you need to carefully prepare everything: materials, tools. Make a list of everything you need in advance and stick to it strictly. Otherwise, the soldering process will turn into a real torment.
Fluxes
The building materials market is represented by a wide range of fluxes for soldering. Many of them are universal and suitable for different purposes. The main role played by thesesubstances in solving the problem, how to properly solder wires to the board with a soldering iron (or for other cases), - prepare materials for the process itself:
- etching core wires;
- oxide film removal.
For different types of metals and their alloys, there are fluxes. At the same time, alkaline mixtures, acids and s alts are included in their chemical composition. All this is actively involved in reactions when a high temperature is reached.
Conventionally, all fluxes can be divided into two main groups:
- active elements;
- "drugs" based on rosin.
Active elements are made on the basis of inorganic acids (hydrochloric or perchloric). They can be used to connect any conductors, including metal parts. It is only worth considering that such a flux adversely affects copper, causing a corrosion process. Therefore, all material residues should be removed immediately after soldering is completed. These elements have increased conductivity, which often causes a short circuit.
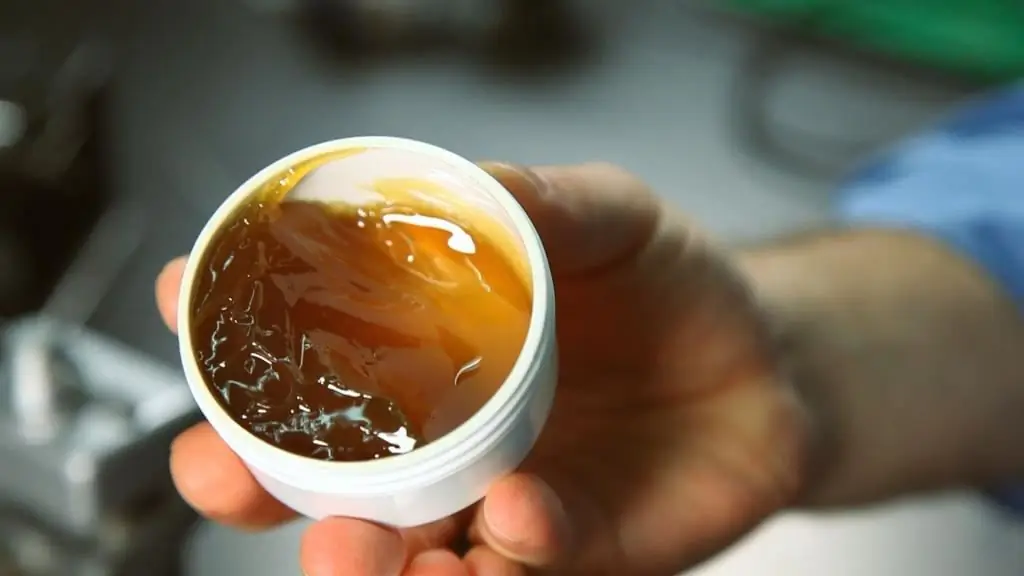
As for preparations with rosin, they may contain alcohol and glycerin, which completely evaporate during the soldering process. Fluxes in liquid form are not as effective, but they are indispensable if you have to work with non-ferrous metals. But it also requires a quick flush. For simpler soldering tasks, pure rosin itself is often used.
Solder Selection
How to solder wires with a soldering iron? Pick up the fluxit's so easy. With the choice of solder, everything is much easier. When working with copper wires, tin-lead alloys of the POS type should be used. The number indicated after the marking corresponds to the content of tin in the solder.
As noted by experts, alloys with a large amount of tin should be preferred. Due to this, the electrical conductivity of the new compound increases markedly. This gives it extra strength.
The inclusion of lead contributes to the normalization of solder hardening. Without this element, cracks can form on the surface of the solder, which ultimately leads to the inevitable destruction of the joint.
Today, other solders can be found on the market, for the manufacture of which modern technologies are used. Lead is replaced by zinc or indium. And since these are non-toxic elements, the alloys are environmentally friendly and safe. The connection itself is highly durable and resistant to corrosion processes.
Therefore, with this option, you don’t even have to bother about how to properly solder the wires with a soldering iron.
Solder paste
On sale, in addition to fluxes and solders, you can find a special paste for soldering. However, it is easy to cook it yourself. To do this, take an enameled dish, where you need to place hydrochloric acid (32 ml), add ordinary water (12 ml), then lower the pieces of zinc (8.1 g). After completion of the dissolution reaction, tin (8.7 g) is added to the composition. Now it remains to wait for the completion of the next reaction. The water is then evaporated until a paste is formed.substance.
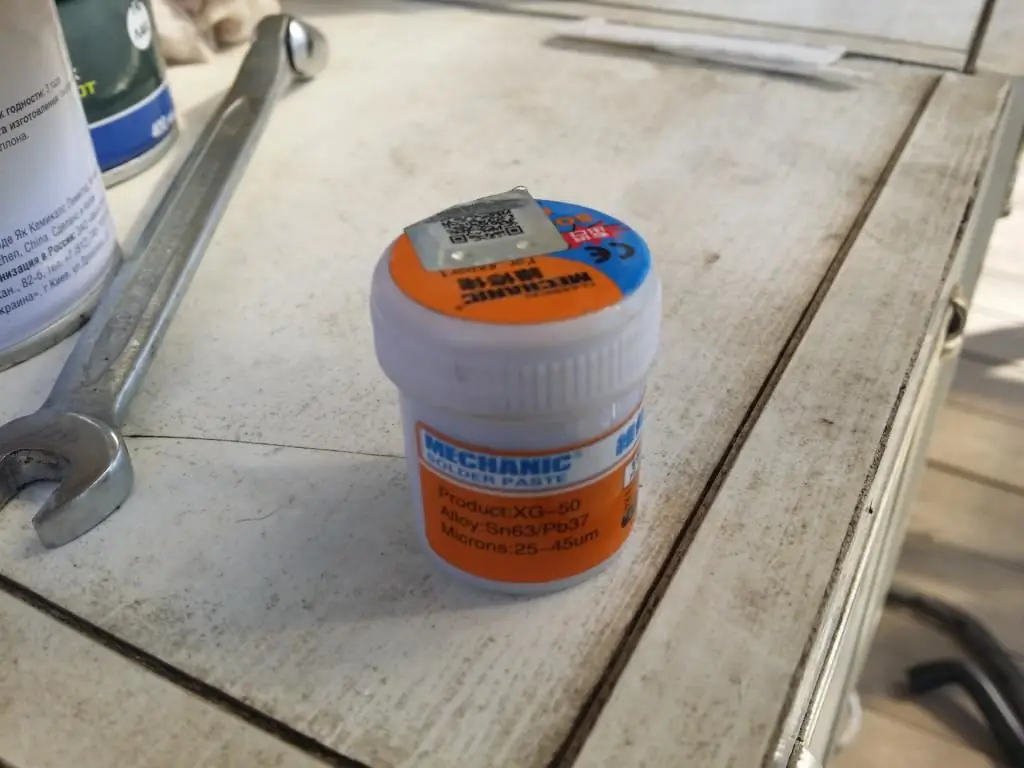
Now you should transfer the composition to a porcelain container and add the crushed elements in the following quantity:
- lead - 7.4 g;
- tin - 14.8 g;
- dry ammonia - 7.5 g;
- zinc - 29.6g;
- rosin - 9.4g;
- glycerin - 10 ml.
It's all warmed up and mixed well.
Paste soldering
How to solder wires with a soldering iron with solder paste? In this case, the following sequence of actions should be followed:
- Wire cores are prepared in a known way, if necessary, they are twisted.
- The paste is applied with a brush in a thin layer.
- The soldering surface is heated with a soldering iron until the paste melts.
- Solder is removed to cool the joint material.
As you can see, there are no significant differences from the usual use of tin here. The paste shows its high efficiency not only in connecting wires, but also in small parts made of metal alloys based on copper or brass.
Features of connecting wires by soldering
In most cases, a general scheme is used, which consists of standard manipulations. It is worth noting that often consumables can have versatility. If necessary, some can be replaced by others. If we are talking about a connection that will subsequently be subjected to significant loads, the technological requirements must be strictly observed! In particular, you need to usecertain materials.
How to properly solder thin wires with a soldering iron? The very essence of the work consists in heating the cores to a high temperature and then connecting them to each other by wrapping them with solder. As the wires cool, the soldering area becomes solid.
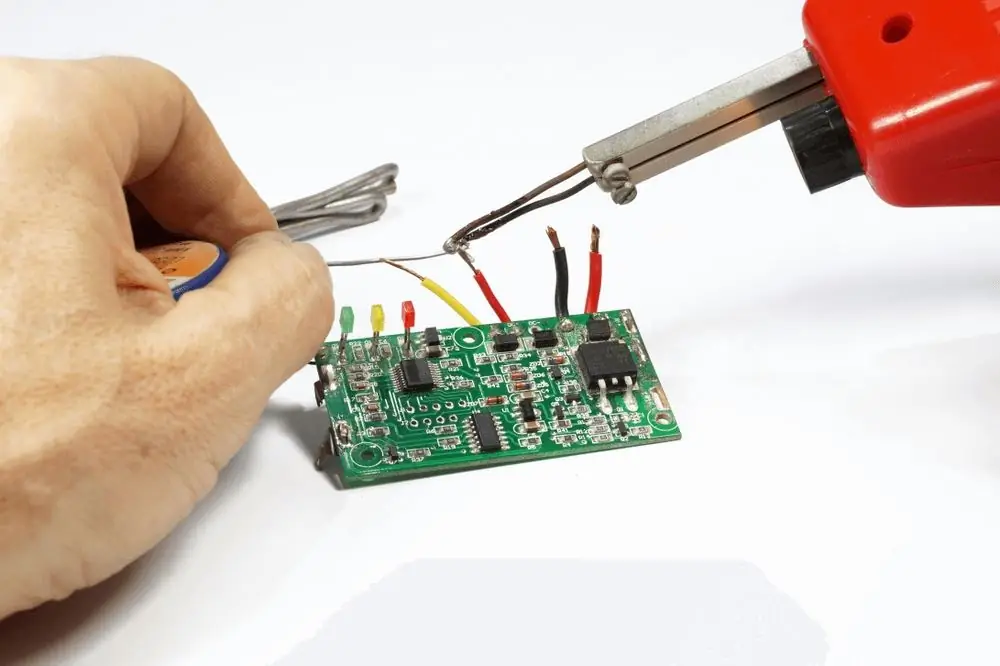
From the point of view of many electricians, such work seems too easy. In fact, when performing this procedure, you can inevitably encounter its specific features. Each specific case differs in the choice of solder. In addition, it is necessary to ensure reliable fixation and immobility of the wires for their connection with solder.
Important point to be aware of
If copper wires are connected to each other using a high-temperature method, then in this case it is necessary to pay special attention to the electrical conductivity and mechanical strength of the soldering point. These parameters are directly dependent on each other.
How to solder wires with a soldering iron with tin? The quality of the wire connection depends on how strong the soldering is. And this in itself provides electrical conductivity at a high level. In this case, the thickness of the deposited solder layer is also important, since it has a high resistivity.
The strength of the connection of copper conductors is largely due to the cleanliness of the soldered surfaces. The solder interacts with the wires at the atomic level. In this regard, not only pollution, but also the presence ofthin oxide film.
Another prerequisite is the temperature of the solder. It should be noticeably lower than the parts to be joined. If materials with a higher melting point are used, then it is impossible to achieve the required bond strength. Its crystal lattice will be formed incorrectly. For this reason, only the correct solder should be used on copper wires.
Soldering procedure
Now let's actually consider the procedure itself, how to properly solder copper wires with a soldering iron.
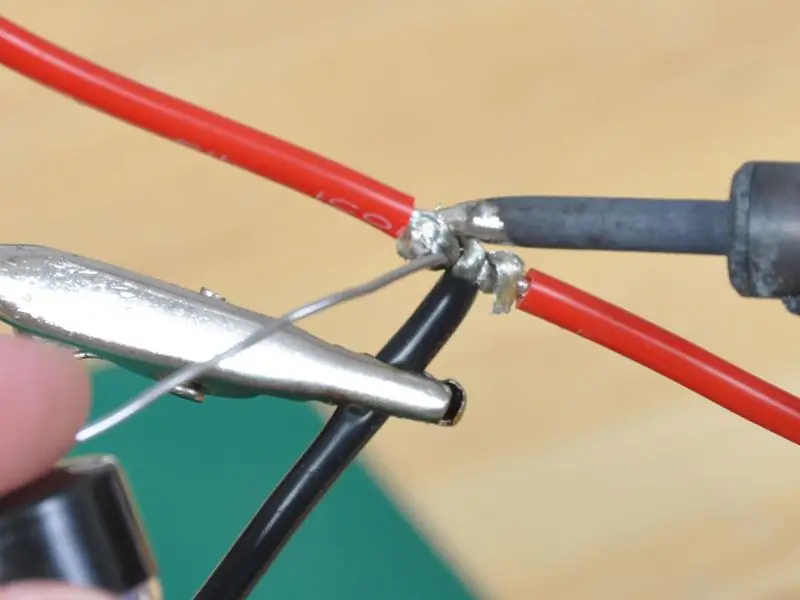
The whole process of such a connection can be conditionally divided into several main stages:
- preparation of conductors;
- tinning;
- connection.
Preparation of conductors
Before soldering conductors or connecting them to a microcircuit, it is worth preparing them for the upcoming operation. To do this, a small area should be freed from insulation. If the cores contain an oxide film, then it must be disposed of. Otherwise (as we already know) the connection quality will be low.
A small piece of sandpaper will do for this purpose. It does not make sense to use a large grain here, so you should limit yourself to small ones. The metal core should shine.
Tinning
Now you can turn on the soldering iron and wait until it heats up to the melting temperature of rosin. When touched with this material, it will actively melt, even with a slighthiss.
Now comes the preliminary stage of the task, how to properly solder the wires with a soldering iron. A core (or several) is taken, brought to the rosin, which is heated with a soldering iron tip. Further, the entire cleaned metal surface is immersed in the molten material so that the core is completely covered with it.
After this process, the actual tinning itself follows. That is, a piece of solder is caught with a sting (more precisely, a drop), and the material is spread throughout the core. It spreads rather quickly and envelops the processed part of the conductor, covering it with a thin layer of new metal.
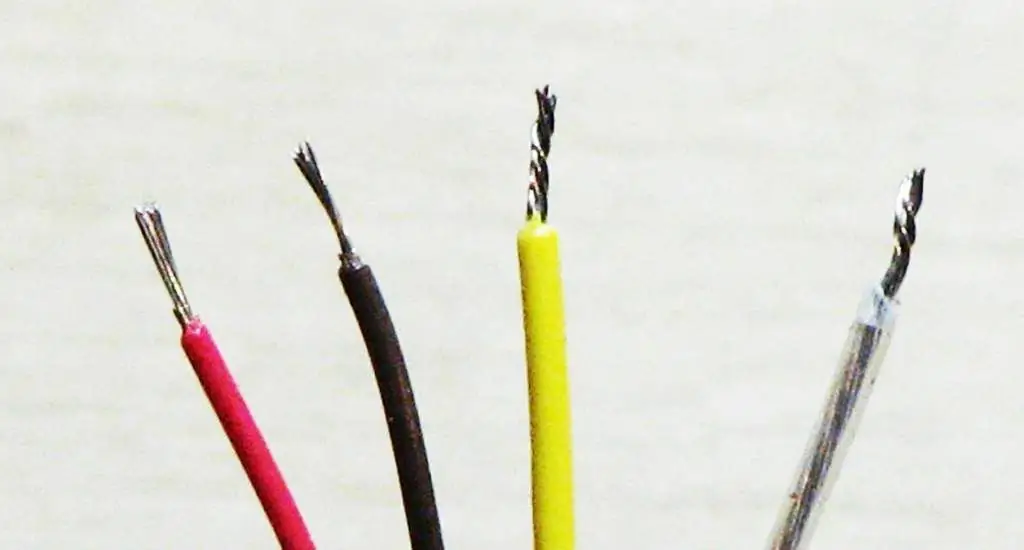
To distribute the solder more quickly, the conductor should be rotated. The natural tone of the veins is gone. A nice silvery color appears. Thus, all wires that are planned to be connected should be processed.
Connection
Actually now comes the soldering process itself. To do this, the conductors are folded together with the cores (one to the other). It is important that at the same time they are close. If the connection affects a large length of the cores, then they can first be twisted together.
Now it remains to grab the solder with a sting. It is pressed against the soldering point. There is no need to make special efforts here, because a drop of metal will melt the tinning material and everything will be connected into a single monolithic link. And when the solder covers the entire junction, the process can be considered complete.
The wires, however, should be kept together for some time to cool the material. To speed up this process, solder can beblow.
Soldering copper wires with aluminum wires
When analyzing the topic of how to properly solder wires with a soldering iron with rosin, it is worth considering such an important point. Under no circumstances should aluminum be combined with other reactive metals directly! And copper just refers to such a variety of materials. Aluminum and copper conductors are not something to be soldered, they cannot even be simply connected to each other by direct contact.
This is due to the fact that these metals have different thermal and electrical conductivity. When a current passes through an aluminum wire, the metal heats up more and expands more due to its qualities. As for copper, although this metal also heats up and expands, it does so much more slowly.
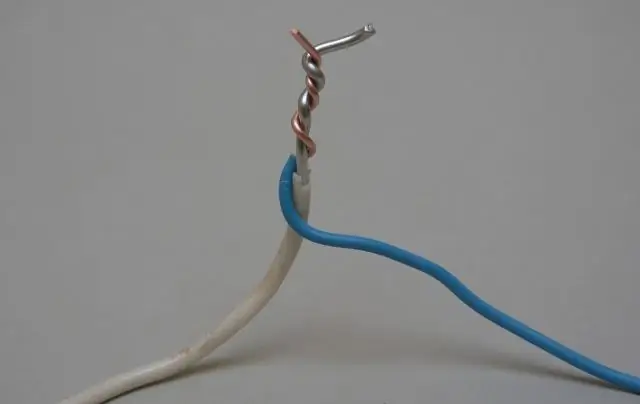
As a result of constant expansion-contraction cycles, contact is broken, and no matter how well it is done. As a result, a film is formed that prevents the passage of current. Therefore, wires made of these metals are not connected directly to each other.