Despite the increased safety requirements at production facilities, it is not yet possible to completely eliminate the risk of fire in workplace conditions. Therefore, the relevance of personal protective equipment against flames remains relevant, which, by the way, are also used in other areas besides industrial ones. The introduction of new technologies makes it possible to improve the quality of materials for workwear. In addition, modern refractory fabric is able to provide not only thermal safety, but also protection from other dangerous influences.
What threats does fireproof fabric protect against?
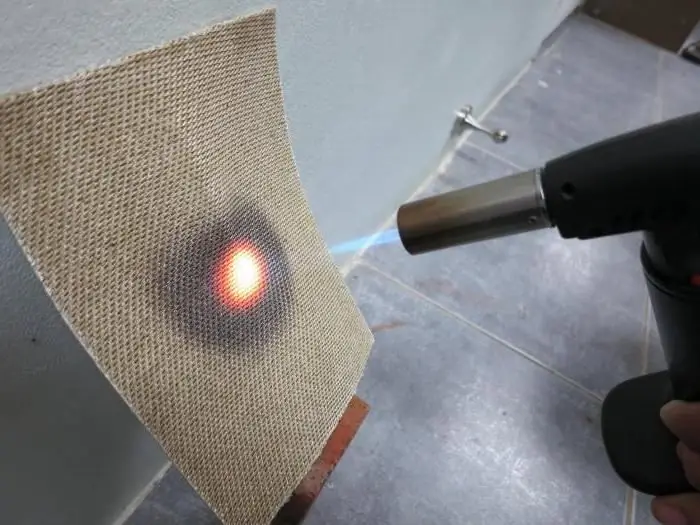
On the market there are less and less specialized fabrics with flame retardant properties that would focus only on providing a barrier in front of the flame. But, despite the increasing popularity of multiprotective materials, experts consider the development of compositions designed for specific properties to be the most promising. In particular, fabrics for overalls at metallurgical enterprises are focused on ensuring safety from thermal effects, open flames, and also from splashes of hot metal. Protect against other hazards are materials made for electrical workers. Events. In this case, protection against electric current is also important. As an additional feature, it is worth noting the resistance to mechanical stress. At the same time, technologists are striving to increase the wear resistance and strength of textiles.
Main characteristics of fireproof fabrics
Almost every workwear manufacturer produces materials using its own technologies, forming unique compositions and, accordingly, technical qualities. One of the most important indicators of the effectiveness of such tissues is the oxygen index (CI), which averages 30-32. Heat resistance indicators are also significant, which determine the ability of the material to maintain its structure under the influence of a flame. Experts have an ambiguous approach to assessing the density of workwear of this type. Usually heat-resistant materials have a density in the range of 170-350 gr/m2. The higher this value, the more effective the mechanical and thermal protection. But this rule does not always work. The best compositions have a low density, but retain optimal protective qualities. The decrease in this indicator is due to the desire to provide comfort in the process of work, since high density increases the mass of clothes, fettering the user.
What is fireproof fabric made of?
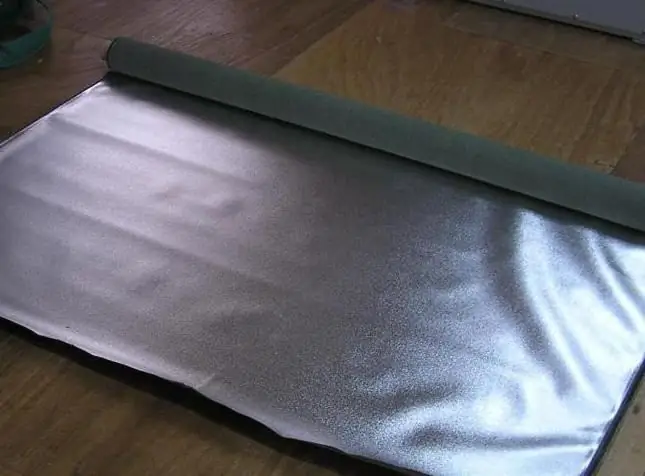
The specific composition of the material depends on the manufacturing technology of the final product. For example, 100% cotton can be used as a base, which is then impregnated or coated with protective compounds. So that the fabric does not supportcombustion, many manufacturers also use chemical retarders of this process, but this component can be hazardous to the he alth of the carrier. More efficient and technologically advanced canvases are initially formed with compositions with the required characteristics. Their structure is usually formed by a fire-resistant fiber with constant performance. For example, the use of heat-resistant viscose allows not only to protect the user from the flame, but also contributes to the regulation of the microclimate under clothing. Special attention is paid to external protection, which is used as a fluorocarbon finish, and fiberglass, as well as other protective components.
Flame retardant treatment
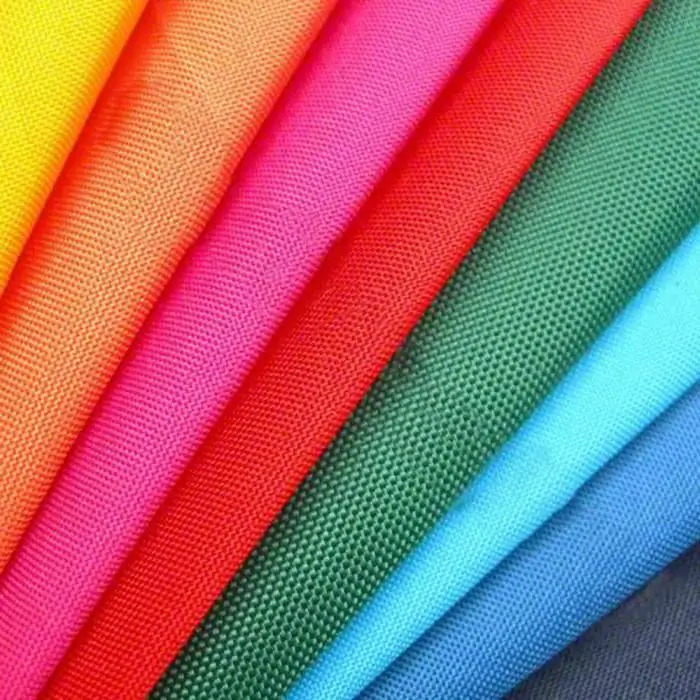
A variety of materials are used for exterior treatment, including silicone coatings, fiberglass cloth and metallized coatings. As for the silicone treatment, it effectively protects during the welding process due to the flexible insulation. Fiberglass fabric also performs well, which usually has a double-sided coating in the form of a polyurethane aluminized layer. The features of this technology include the inclusion of steel wire by the method of reinforcement. The result is a flame retardant fabric with flame retardant functions and high mechanical resistance. An alternative to this treatment is a fiberglass base treated with aluminum foil. As a rule, the application is carried out on one side, which, however, does not reduce the technical and operationalmaterial qualities. Such fabrics are used both as part of overalls and for thermal insulation of pipelines.
Refractory impregnation of fabrics
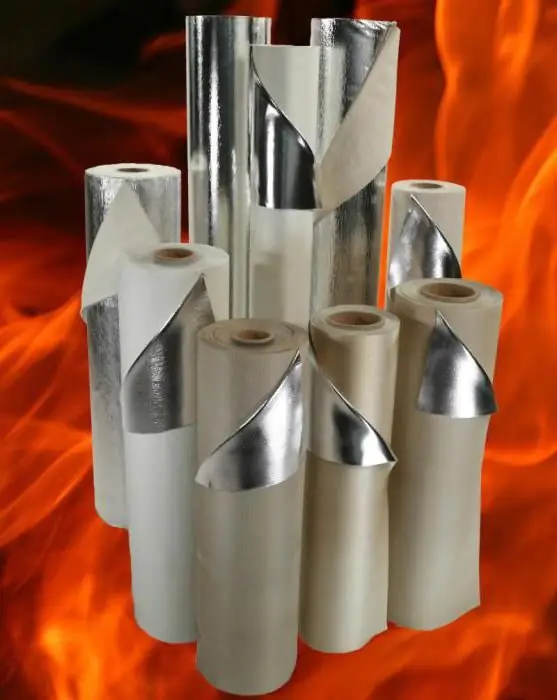
Usually, technologies are also used as impregnations that allow metallizing the fabric in order to protect it from thermal effects. Nowadays, vacuum semi-carbon processing is used, which protects the worker not only from an open flame, but also from melts of various metals. This is the reason for the purpose of the paintings. As a rule, the fabric impregnated with a refractory composition is used in the metallurgical industry. It is noteworthy that the methods of fabric metallization due to aluminum have been used for more than a decade. But modern technologies make it possible to create highly efficient and easy-to-use canvases. According to reviews, workwear with metallic impregnation is characterized by a soft structure, lightness and elasticity.
Multi-protective fabrics
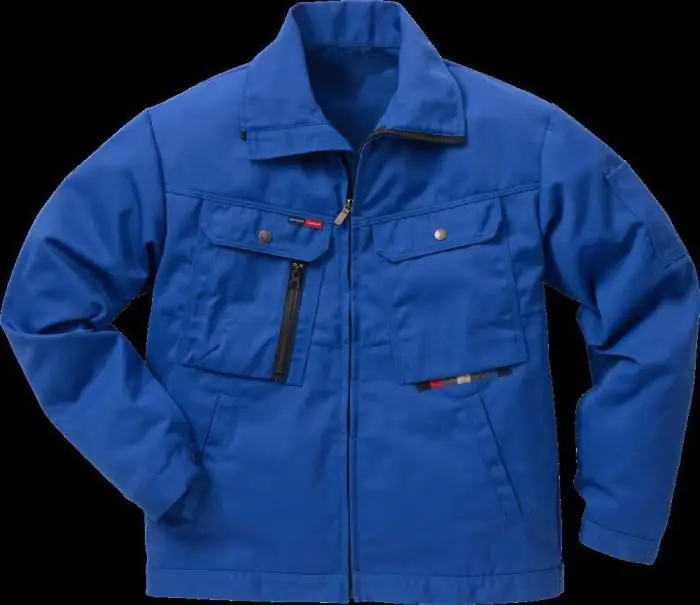
As already mentioned, truly high-quality material with protective functions can only be obtained with a focus on a certain range of threats. Despite this, there is a significant demand for universal materials, which include fire-resistant fabric with multi-protection. First of all, clothing made from such textiles protects the worker from all types of thermal effects in various industries. Manufacturers also strive to endow materials with resistance to chemical and mechanical stress. Among the additional featuresmulti-protective fabrics include UV neutrality, signal shade durability and thermoregulation function.
Features of aramid fabrics
Aramid fibers have formed a whole group of fabrics that have fairly high technical and operational properties. Based on synthetic polyamide, technologists develop structures for high-strength and heat-resistant fabrics. Moreover, these qualities do not mix, but go in parallel in different products, depending on the fibers used. Another thing is that a set of overalls can include both materials. At the moment, the production of aramid fabrics makes it possible to provide the consumer with fibers that are not inferior in strength to steel sheets. This material is marketed under the Kevlar brand. But it is important to consider that such products have a significant drawback - they do not tolerate direct exposure to sunlight and are subject to photodecomposition processes. Heat-resistant aramid fabrics that can withstand temperatures of about 400 ° C also show worthy qualities.
Where is flame retardant fabric used?
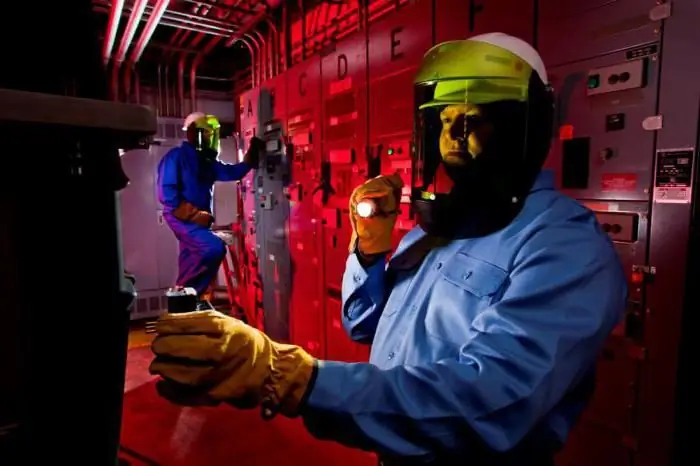
The range of applications for such materials is almost limitless - wherever fire protection is required, fire-resistant canvases find a place. Of course, the issues of personal protection are most relevant for manufacturers. These are areas in which it is required to ensure the safety of workers in contact with hazardous, from the point of view of thermal exposure, objects and materials. Recently, refractory fabric has also become widespread,which can be used as a finishing material. Along with the primary function of flame protection, such textiles also provide a decorative effect, allowing you to maintain the stylistic advantages of the interior.
Conclusion
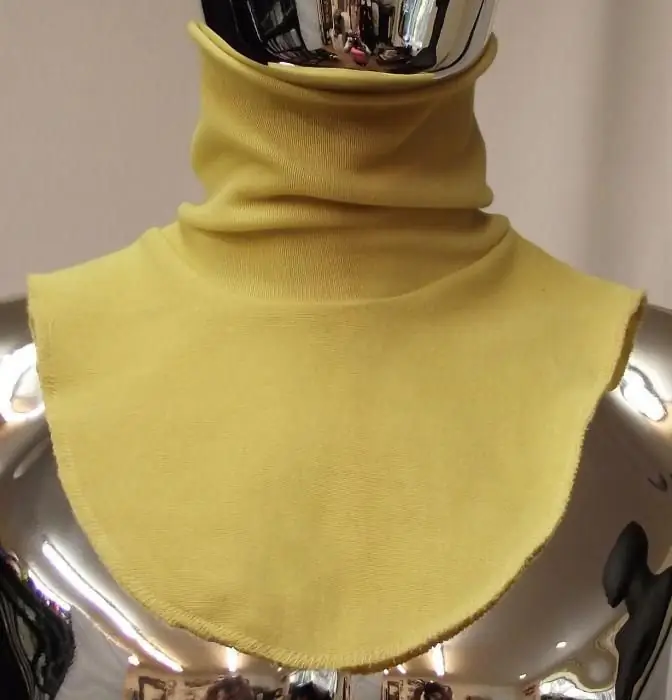
Providing protection against thermal burns today is not particularly difficult in terms of implementation. The market is oversaturated with offers of various properties, allowing you to choose the right material for both domestic use and industrial facilities. At the same time, refractory fibers and fabrics for workwear are distinguished by different qualities that go beyond thermal protection alone. Manufacturers produce combined textile materials designed for specific industries. Multifunctional fabrics are also gaining popularity, which can be used as a protective agent against a wide range of threats - from direct fire to chemical reagents.