Aluminum is one of the most demanded metals due to its high quality characteristics. Its main area of application is industry. Aluminum alloys are also used, namely duralumin. This compound got its name in honor of the Dural company, in which the production of the alloy was first established. According to experts, welding of duralumin is considered a rather laborious process. You will need to be as focused and attentive as possible. You will learn how to weld duralumin at home in this article.
Introducing the connection
Before you start welding duralumin, you should know about the basic parameters of this alloy. Duralumin with a maximum fluidity of 250 MPa has a density ranging from 2.5 to 2.8 t/cu. m. Melts attemperature of 650 degrees. Such an indicator is inherent directly in aluminum itself. This explains why during welding, duralumin begins to flow due to rapidly melting electrodes.
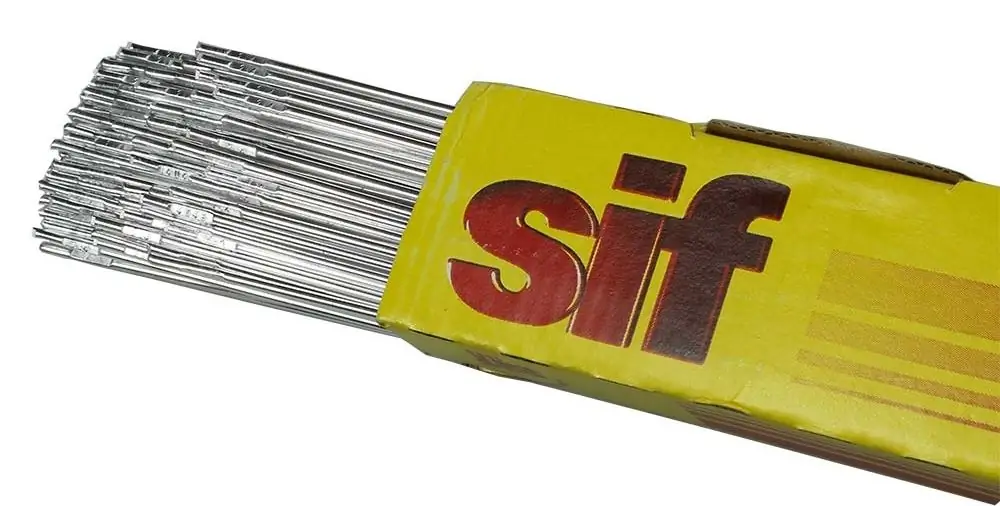
What is the difficulty of the procedure?
Judging by the numerous reviews, complications are not excluded during the welding of duralumin. The reason for this is the technical characteristics of the alloy, which contains aluminum (93.5%), manganese (0.5%), magnesium (1.5%) and copper (4.5%). According to experts, their connection with each other is bad. Therefore, it is better that welding work with duralumin is performed by an experienced person. If you have a need to connect parts from this alloy, you will have to take into account some of the nuances, more on which below.
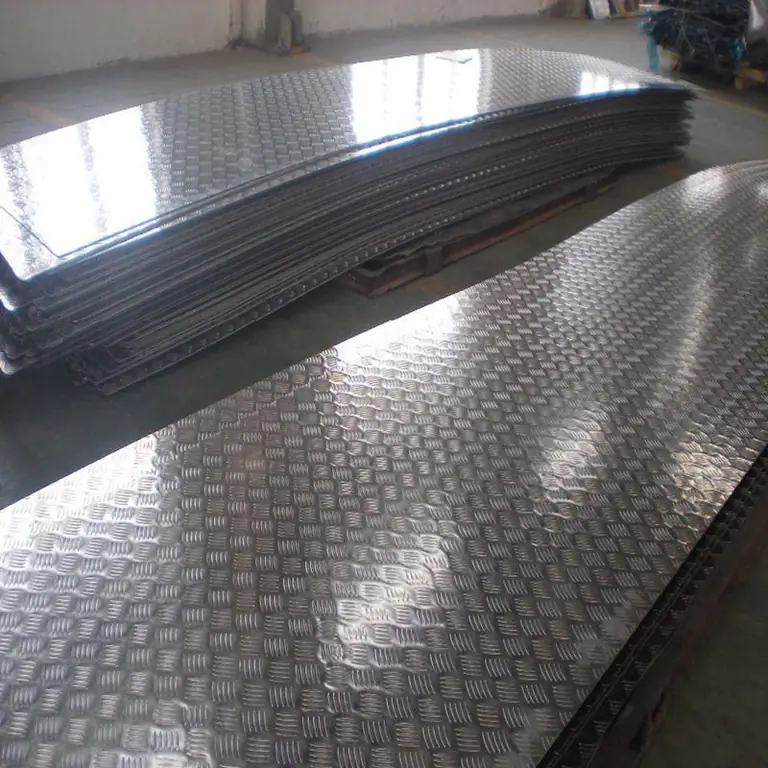
About ways
Connection can be made using semiautomatic devices. The device for welding of duralumin works in a pulsed mode. Thus, the metal is heated under the influence of pulses, and after a drop enters the weld pool, a seam is formed. If you decide to stop on this method, you should know that the constant negative polarity on the electrodes will not give a seam. Only positive is needed.
The second way is to use tungsten-coated electrodes. This method will provide a high-quality and neat seam. To prevent the formationoxide film, use argon.
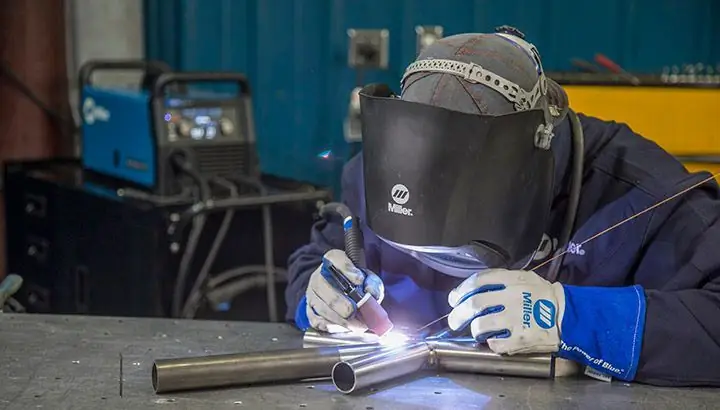
Also, the formation of a gas protective environment is carried out using xenon, krypton and nitrogen. However, these gases, unlike argon, will cost you more. In order to weld products with a thickness exceeding 30 mm with tungsten electrodes in one pass, a three-phase arc must be used. Conventional connection is mainly used to connect surfaces with a thickness of not more than 3 mm.
If you do not have the opportunity to perform an electric arc, use cold welding for duralumin. First, you should get a special composition, namely a two-component adhesive. It can be a thick liquid or mastic.
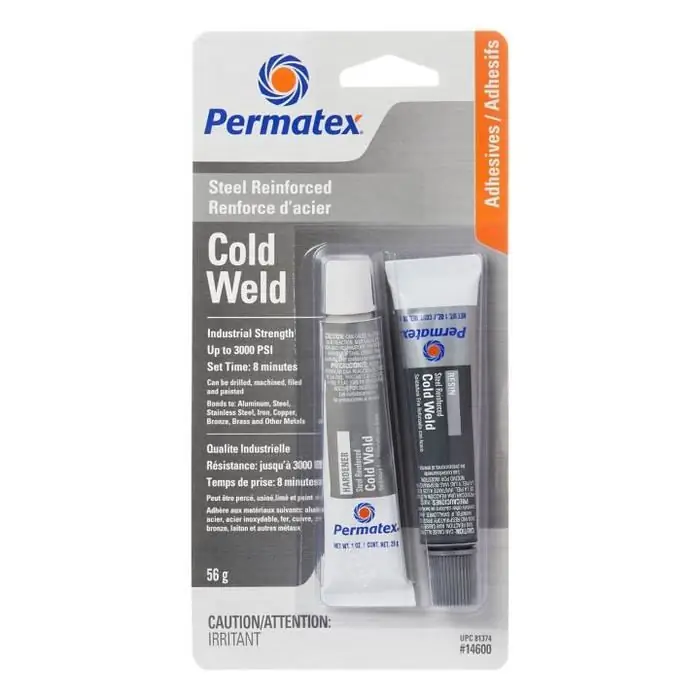
It contains epoxy resin and steel powder, which makes the bond formed stronger. In addition, to improve the characteristics of cold welding, namely, to increase adhesion between parts and resistance to aggressive environments, manufacturers fill adhesives with special additives. This method is also called soldering. The fact is that you can connect the parts without electricity. All you need is a portable gas burner and NTS-2000 solder in the form of a wire. Closing gaps or connecting duralumin parts is easy. It is necessary to heat the part so that the solder with the rod begins to melt and begins to flow into the slot.
Preliminary, the oxide is removed from the surfacesfilm. Unlike previous methods, cold welding is much faster. Predominantly, by means of these adhesive compositions, various emergencies are quickly eliminated when it is necessary to quickly connect parts made of aluminum or its alloys. Judging by the reviews, most home craftsmen prefer this method.
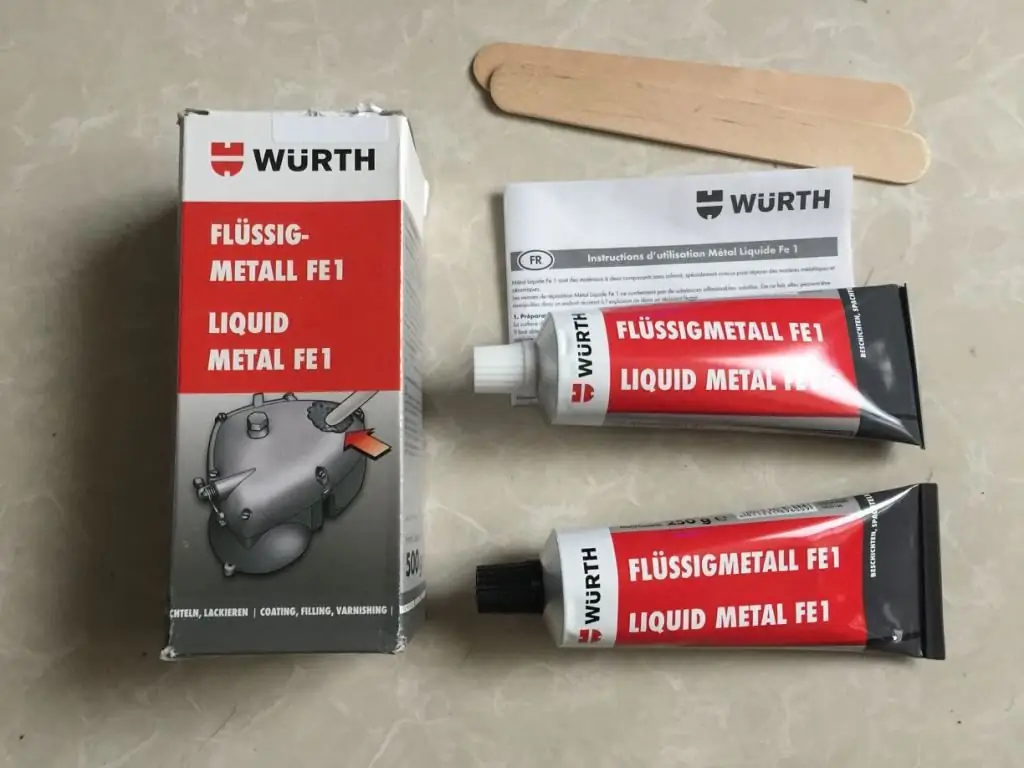
On virtues
Despite the fact that the welding technology is quite complicated, if you do everything right, you will end up with a smooth and high-quality seam. The advantage of this alloy is that, with a fairly small mass, it can withstand a large load. Judging by the numerous reviews, welding of duralumin with argon is considered quite popular. Also, the connection can be carried out using a semi-automatic device. The choice of the most optimal option depends on the master. According to experienced welders, when dealing with this alloy, there are never problems with the choice of electrodes. The fact is that many of them can interact well with duralumin. For example, you can use such brands as OK96.20, OZA-1, OZANA-1, OZANA-2 and OZANA-2.
About shortcomings
According to experts, low resistance to corrosion is inherent in duralumin. This figure becomes even lower after welding. When welding, you will have to be very careful, since the slightest inaccuracy will adversely affect the quality of the connection. Due to the bigthe fluidity of the alloy, it will not be easy to form a seam. To simplify this procedure and speed up the process, experienced welders use flux. It must be applied to the surface of the parts to be joined. As a result, the quality of the connection will be higher. In addition, the seam will be protected from aggressive external influences.
Where to start?
Begin welding with the preparation of workpieces. Various contaminants are thoroughly cleaned from the metal surface and degreased. You can work with sandpaper of various grain sizes or a metal brush. Fats are effectively eliminated with acetone or solvent. After stripping and degreasing, you should take care of the edges, in place of which the seam will be located in the future. If it turns out that your blanks with edges of more than 4 mm., Then they need to be beveled a little. An angle of no more than 35 degrees is considered optimal.
Second step
At this stage, flux is applied. It is important that it covers the welding area evenly. To prevent deformation of the metal, it is first subjected to slow and gradual heating. At the end of the procedure, the seam itself is heated. The joint you form will be covered in slag. It must be carefully knocked down. This recommendation should not be neglected, since cracks are very often under the slag. As a result, the connection will have a very low resistance to stress.
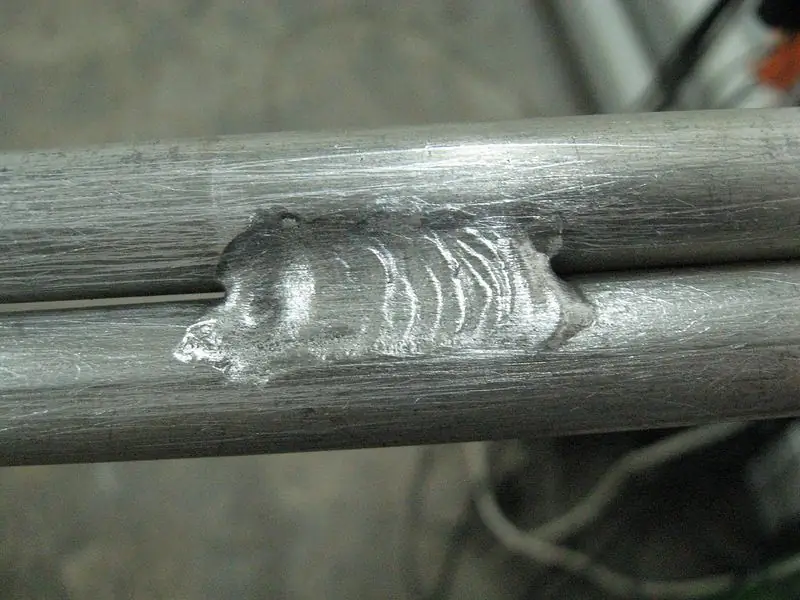
What else will experts advise?
Experienced craftsmen recommend using forwelding duralumin additive. This product is presented in the form of a strong and rigid lamellar rod. Judging by the reviews, with an additive, the metal will be used more economically, and the strength characteristics of the structure will be higher. When working with this alloy, as with any other metal, safety precautions should be followed. Before you start welding, purchase a special protective suit, mask and gloves.